Items |
---|
| | Bitumen | | | Crude Oil Diesel Lubricant Gasoline Napalm | | | Projector Lubricant Can | | | Motorboat Reinforced Hull Icebreaker Bow Expanded Fuel Tank Maneuvering Rudders Emergency Paddles |
Advertisement  IntroductionDevelopment of dhm, dhm characteristics, dhm energy efficiency, dhm applications, turbodrill and screw motor: development dialectics. - Split-Screen
- View This Citation
- Add to Citation Manager
- Get Permissions
- Search Site
Simonyants, Sergey L. "Turbodrill and Screw Motor: Development Dialectics." Paper presented at the SPE Russian Petroleum Technology Conference and Exhibition, Moscow, Russia, October 2016. doi: https://doi.org/10.2118/182147-MS Download citation file: - Ris (Zotero)
- Reference Manager
In Russia oil and gas wells are mainly drilled with downhole hydraulic motors (DHM). In the second half of the 20th century turbodrills, which are high-speed downhole motors, found wide application in large-scale drilling in Volga-Ural region, and further in Western Siberia. The most commonly used type of rock-cutting tool was a tricone bit with "open" bearings working in high-speed mode. Also, diamond bits were used to penetrate deep hard rocks. More than 80% of wells were drilled with turbodrills at that time. Putting into practice tricone bits with sealed oil-filled bearings required application of low-speed downhole motors, so downhole screw motors now dominated as a bit drive in large-scale drilling, which was also boosted by the introduction of high performance PDC bits. Compared to high-speed turbodrills, downhole screw motors are low-speed motors with increased torque, they are also known as Positive-displacement motors (PDM). Comparison of turbodrill and PDM energy characteristics shows that turbodrill has a so-called "soft" torque dependence on rotation speed, whereas in PDM it is "hard". That is why with PDM, drilling mode parameters are more stable. On the other hand, in the process of drilling and downhole motor wear turbodrill energy characteristic does not change much, whereas PDM demonstrates significant decrease of energy parameters. Furthermore, the level of lateral vibrations generated by PDM is also high, which has a negative effect on the wellbore quality. Turbodrill and PDM differ essentially, each having specific advantages and drawbacks. However, they are technical means of one and the same drilling method. Today, each type of DHM has its own area of effective application. Traditionally, the turbine drilling method called today "Well drilling with downhole hydraulic motors" has been the main method of drilling oil and gas wells in Russia. The relative volume of its application is more than 90%, where screw motors account for 70% and turbodrills account for the rest ( Fig. 1 ). 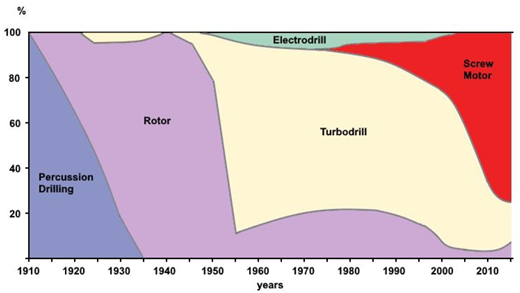 Relative application volumes of oil and gas well drilling methods in the USSR and Russia There are two main types of modern downhole hydraulic motors, turbodrills and screw motors, which differ essentially, each having specific advantages and drawbacks. However, they are technical means of one and the same drilling method. Today, the areas of effective application of turbodrills and screw motors are distinguished. Turbodrills are high-speed downhole motors with a rotation speed of 500 – 1200 rpm used mainly with scraping diamond bits and with roller bits with "open" bearings. Screw motors are low-speed motors with a rotation speed of 90-300 rpm used for work with roller bits with sealed oil-filled bearings and cutting-chipping PDC bits ( Fig.2 ). 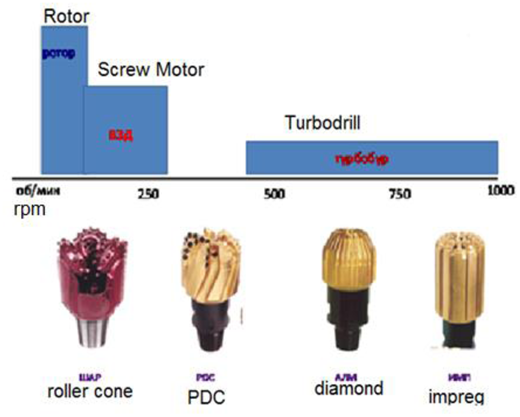 Applications of bits and downhole hydraulic motors But this has not always been the case. The development of technical means for turbine drilling was accompanied by a strong competition between the two approaches and the problem "What is better: turbodrill or screw motor?" was being solved in laboratories and oil fields. The problem was not only concerned with different types of bits and drilling modes but also with the accuracy of drilling according to the predetermined trajectory. Much shorter screw motors (8-10 m) allowed installing telemetry measurement systems substantially closer to the bit in comparison with standard turbodrills (27-30 m), which explains the domination of screw motors in modern drilling conditions. The evolution of bottom drives to rock cutting tools can be looked at from the perspective of the struggle of two conceptions – high-speed and low-speed drilling methods, which reminds of the dialectical unity and struggle of opposites. For Socrates, dialectic is discovering truth through contradiction of opposite views. Any development process has positive and negative sides by virtue of the dialectical unity of opposites . Struggle of opposites and elimination of contradiction plays a crucial role in technical and technological development. Dialectical development of technologies is a contributing factor in the natural improvement of technical means productivity and implies an unbiased transition to more sophisticated cutting-edge technologies [ 1 ]. Dialectical development of drilling equipment, including downhole hydraulic motors, has resulted in the invention of modern turbodrills and screw motors which have high indicators of energy efficiency, reliability and utility, and with which it is possible to realize the boldest projects in drilling oil and gas wells in various geological conditions. In the early 20 th century the rotary drilling method almost replaced the widely used percussion drilling method. Transfer of power from the rotor to the bit through a long and flexible drill string allowed significant drilling speed increase, though it had some obvious drawbacks, the main one being pipe failures. In drilling deeper wells pipe failures became more frequent. At about the same time it was decided to install a motor for rotation transfer directly above the bit. Attempts to design a downhole hydraulic motor consuming mud flow energy to actuate the rotary bit drive were made in different countries but were not successful. Ingenious inventions of hydraulic rotational mechanisms by Brandt (Switzerland), Cross, Westinghouse, Scharfenberg, Diehl (the US), Simtchenko, Valitsky (Russia) and other engineers did not have practical applications. The same was true of bottomhole hydro-percussion mechanisms, the so-called "drilling rams", developed by Volsky, Prushcovsky [ 2 ]. In 1922 a Soviet engineer M.A. Kapelyushnikov developed a turbodrill which consisted of a one-stage turbine and an oil-filled gear box. In 1924 this turbodrill drilled the first well 600 m deep with high speed performance. The Kapelyushnikov turbodrills were used in the next decade, but owing to low reliability the turbine method eventually gave way to the rotary drilling method [ 2 , 3 ]. In 1934 Experimental Turbine Drilling Bureau was established and the leading experts P.P. Shumilov, R.A. Ioannesyan, E.I. Taguiyev, and M.T. Gusman put a lot of effort into improving on turbodrill design. To overcome the drawbacks of the Kapelyushnikov turbodrill (one-stage turbine and gear box) they invented a direct-drive turbodrill with multistage axial-flow turbine. The principles of the direct-drive multistage turbodrill design were basic to the further development of turbodrill manufacturing, and the design engineers' theoretical insights and assumptions made it possible to develop the modern theory of turbine drilling. The development of turbodrills with multistage turbine made the turbine drilling method the most widely used for oil and gas well construction in the USSR and Russia. The advantages of turbodrills over the rotary drilling method were significant: Fewer pipe failures. Substantial increase of drilling speed. Far better possibilities for directional drilling. Since 1953 dozens of ingenious turbodrill designs were developed in Moscow, at VNIIBT, which was a major scientific and design centre engaged in turbine drilling equipment and technology. Those were general purpose turbodrills used in large-scale drilling in Volga-Ural region, in Western Siberia, etc., as well as turbodrills for drilling in specific conditions: turbodrills with rolling bearings for drilling deep wells using increased density drilling mud; turbodrills with hydrodynamic braking system for work with roller bits with sealed oil-filled bearings; turbodrills with hollow shaft providing high differential pressure in the bit; turbodrills with rotating body providing wellbore verticality; turbodrills with vibration dampening system; turbodrills for core sampling; turbodrills for work with diamond bits; heat-resistant turbodrills for drilling in geothermal conditions; retrievable turbodrills for drilling without pulling the pipes, including casing for drilling with casing; turbodrills for reactive turbine drilling (rotary turbine drilling) of larger diameter (up to 5 m) wellbores, and others [ 2 ]. Turbodrills developed at VNIIBT had increased rotation rates of 500 – 800 rpm. In drilling relatively shallow wells (up to 2000 m) the turbine method provided high penetration rate compared to the rotary method. However, deeper drilling required bit rotation rate drop. The main method of turbodrill energy parameters optimization was adding stages to the axial-flow turbine. Turbines now consisted of two or three sections which were assembled on the drilling floor. Turbodrill axial bearing was installed in the spindle section. The widespread deployment of turbodrills in the 20 th century was accounted for by the fact that tricone bits with "open" bearings were mainly in use at that time. However, in the late 1960s tricone bits with sealed oil-filled bearings gave the rotary method a competitive advantage over other methods. A low-speed bottom drive had to be developed. Numerous attempts to develop low-speed gearless turbodrills were not successful. Though turbodrills with oil-filled gear box were developed at VNIIBT Perm branch, they did not find wide application because of structural and maintenance complexity. It was in the 1960s that the problem was solved by VNIIBT experts M.T. Gusman, S.S. Nikomarov, Yu.V. Zakharov, V.N. Menshenin, N.D. Derkach who developed essentially different positive displacement downhole motors (PDM) with multi-lobe gerotor mechanism. It should be mentioned that in a wide range of hydrostatic (positive displacement) mechanisms only those motors proved effective in well drilling [ 4 , 5 ]. This invention contributed in keeping dominant position of downhole hydraulic motors in drilling oil and gas wells in Russia. The operating part of screw motor is multi-lobe rotor and stator couple, where rotor makes eccentric planetary rotation inside rubber-covered stator. Modern multi-lobe screw motors provide a bit rotation rate of 90 – 300 rpm. Being short and having energy characteristic which is more suitable for work with PDC bits and tricone bits with sealed oil-filled bearings, screw motors are far ahead of conventional three-section turbodrills. The development of turbodrills and screw motors was not the same, but today there is a uniform conceptual approach to downhole hydraulic motor design. It is a short (8-15 m) downhole motor with a high power operating part (multiple stage turbine or rotor – stator couple), provided with inclination unit with controlled axes twist angle, replaceable centralizers and other tools necessary for its effective performance. The prototypes are shown in Fig. 3 . Downhole motor service life is to be comparable to time needed to drill of predetermined interval. Today, such downhole hydraulic motors are manufactured by the US, Russia and China manufacturers. 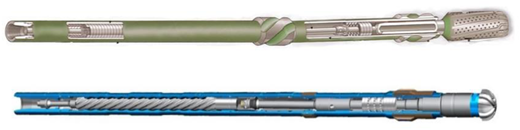 Turbordrill (from Neyrfor Schlumberger Catalog) and Screw Motor (from Radius-Service Schlumberger Catalog) Downhole hydraulic motor is a mechanism in which energy of the drilling fluid flow is converted into mechanical energy of shaft rotation. Part in which energy conversion takes place is called DHM operating part. In the process of conversion energy can be lost both in operating part and in DHM main units. Today, there exist downhole hydraulic motors of various types and designs which have different characteristics. But they all have one thing in common being energy source, which is the forced drilling fluid (mud) flow injected by drilling pumps through drill string into DHM and further into the bit. The main purpose of these motors is to be an effective drive to drill bit. That is why their most important characteristic is energy characteristic which represents aggregate of dependences of the torque, rotation rate, pressure drop, power, and efficiency factor, which characterize downhole motor operating mode. Energy characteristic is to provide drill bit operation within optimal drilling practices parameters. Only in this case maximum technical-economic indicators of well construction can be obtained. Modern downhole hydraulic motors also provide high quality well construction. Their design and energy parameters are to ensure drilling according to the specified trajectory in order to obtain the predetermined wellbore profile. Turbodrill energy characteristic is shown in Fig. 4 . It is visible that rotation rate is highly dependent on torque curve. Since the torque can be tested, on top of everything else, by value of weight-on-bit, and the WOB is continuously changing, there is some uncertainty when setting bit operation mode, which is a drawback of turbodrill torque characteristic. 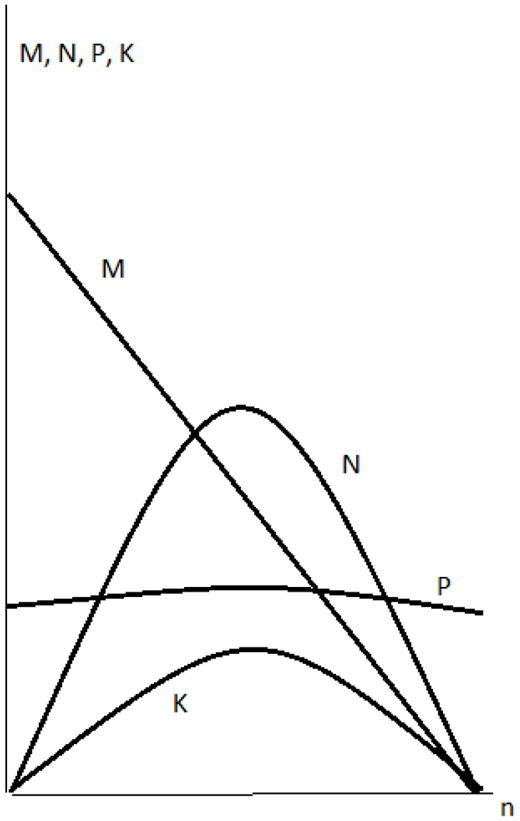 M – torque; n – rotation rate; N – mechanical power; P – pressure; K – efficiency factor. Screw motor energy characteristic is shown in Fig. 5 . It can be observed that rotation rate of screw motor is almost independent of torque curve, which allows reliable identification of the bit operation mode and is an advantage of screw motor torque characteristic. 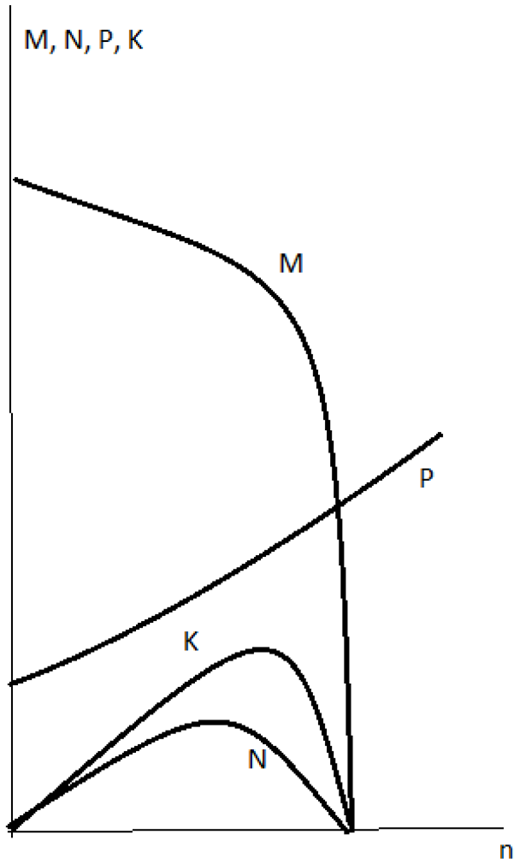 The above mentioned is related to the characteristics of new (not worn) DHM. However, in well-worn motors these characteristics are changed significantly. Fig. 6 shows torque-wear curve in DHM of two types. We can see that while turbodrill energy parameters decrease slightly, in the case of PDM drive this decrease is quite obvious. It is caused by difference in the nature of wear of operating parts of turbodrill and those of screw motor. If turbodrill is run as required multiple stage turbine's service life is up to 1,500-2,000 hrs before it is replaced, with no danger of strong influence of stator and rotor flow channel erosive wear on turbodrill energy characteristic. 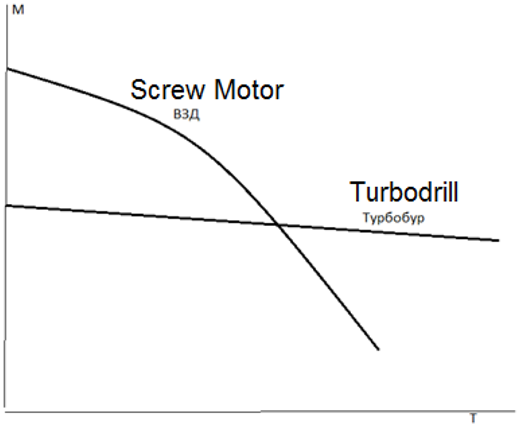 M – DHM braking torque; T – DHM operating time. As regard to the rotor-stator couple, continuous friction of metallic rotor against rubber stator leads to the inevitable wear of the surface of these parts, formation of clearance between them, and has a negative effect on energy parameters of screw motor. Despite the fact that the specified service life of rotor-stator couple is 200-250 hrs, in reality they are contradictory and could be in the range from 40 to 400 hrs. Such a great difference in wear indicators is most likely to be caused by different drilling conditions, operation technologies, drilling fluids used and design of operating parts. The gerotor mechanism starts to wear best in the first 50-80 hrs of work in the well. It is accounted for by strong hydro-mechanical resistance in operating parts in running of helical surfaces of stator and rotor under action of radial forces caused by increased initial rotor-stator diametrical interference. In spindle sections of turbodrills and PDM manufactured in Russia axial bearings of two types are usually installed: sliding rubber-metal ones or rolling thrust ball bearings. These bearings' uniform wear rate is about 0.02 – 0.04 mm per hour of DHM operation. If sliding axial bearings with PDC material are applied, wear rate can be reduced more than by an order greater. Axial and radial bearings wear has a negative effect on energy characteristics of both turbodrill and screw motor and makes their performance much worse. Vibrations of DHM during operation influence general dynamic behavior of drill string in the well and of bit in place. DHM generate vibrations of all types: longitudinal, torsional and lateral. Longitudinal vibrations occur because of the clearance in axial bearing of motor, which appears in the process of wear and can reach 5-10 mm. Torsional vibrations are caused by the dynamics of reactive torque on downhole motor body. Lateral vibrations may be caused by lack of balance of its shaft against body during radial bearings wearing. Lateral vibrations may be caused by lack of balance of its shaft against body during radial bearings wearing. PDM lateral vibrations are constantly accompany its operation because of the eccentric planetary rotation of rotor in stator. Lateral vibrations are the most dangerous since they have a negative effect on bit performance and increase its wear rate. The efficiency of drill bits is in much determined by mechanical penetration rate which directly depends on bit mechanical power value. The higher the mechanical power, the bigger is a penetration rate indicator. where N m – bit mechanical power, Wt; M – bit torque, N·m; n – bit rotation rate, rpm. Mechanical power values for different types of drill bits of one diameter 311.1 mm (12 ¼″) calculated from formulas of [ 6 ] are taken as an example and shown in Table 1 . Rotation rate is accepted as recommended [ 6 ]. As we can see the highest torque of 8,700 N·m is required for PDC bit which breaks the rock through cutting and chipping at a low rotation rate of 200 rpm. Also, high torque of 7,000 N·m can be observed with roller bit, which is likewise accounted for by a low bit rotation rate of 150 rpm. Diamond bit torque is minimal – 3,500 N·m – owing to a high rotation rate of 900 rpm. DHM energy parameters Parameters . | Nomenclature . | . | . | . |
---|
Bit type . | . | Tricone . | Diamond . | PDC . |
---|
Diameter, mm/inch | D | 311,1 12 ¼ | 311,1 12 ¼ | 311,1 12 ¼ | | | | | | Fluid flow, m /s | Q | 0,06 | 0,06 | 0,06 | Fluid density, kg/m | ρ | 1200 | 1200 | 1200 | Rotation frequency, rpm | n | 150 | 900 | 200 | Axial load, kN | G | 250 | 100 | 100 | Torque, N·m | M | 7000 | 3500 | 8700 | Mechanical power, kW | N | 110 | 330 | 182 | | | | | | Diameter, mm/inch | D | 240 9 ½ | 240 9 ½ | 240 9 ½ | Length, m | L | 10 | 10 | 10 | Braking torque, N·m | M | 16000 | 8000 | 18000 | | | | | | Torque, N·m | M | 7000 | 3500 | 8700 | Rotation rate, rpm | n | 150 | 900 | 200 | Mechanical power, kW | N | 110 | 330 | 182 | Pressure drop, MPa | P | 6,5 | 10,0 | 8,5 | Hydraulic power, kW | N | 390 | 600 | 510 | Operating mode efficiency factor, unit share | K | 0,28 | 0,55 | 0,36 | Energy efficiency factor, unit share | K | 2,8 | 5,5 | 3,6 |
Parameters . | Nomenclature . | . | . | . |
---|
Bit type . | . | Tricone . | Diamond . | PDC . |
---|
Diameter, mm/inch | D | 311,1 12 ¼ | 311,1 12 ¼ | 311,1 12 ¼ | | | | | | Fluid flow, m /s | Q | 0,06 | 0,06 | 0,06 | Fluid density, kg/m | ρ | 1200 | 1200 | 1200 | Rotation frequency, rpm | n | 150 | 900 | 200 | Axial load, kN | G | 250 | 100 | 100 | Torque, N·m | M | 7000 | 3500 | 8700 | Mechanical power, kW | N | 110 | 330 | 182 | | | | | | Diameter, mm/inch | D | 240 9 ½ | 240 9 ½ | 240 9 ½ | Length, m | L | 10 | 10 | 10 | Braking torque, N·m | M | 16000 | 8000 | 18000 | | | | | | Torque, N·m | M | 7000 | 3500 | 8700 | Rotation rate, rpm | n | 150 | 900 | 200 | Mechanical power, kW | N | 110 | 330 | 182 | Pressure drop, MPa | P | 6,5 | 10,0 | 8,5 | Hydraulic power, kW | N | 390 | 600 | 510 | Operating mode efficiency factor, unit share | K | 0,28 | 0,55 | 0,36 | Energy efficiency factor, unit share | K | 2,8 | 5,5 | 3,6 |
Besides, energy characteristics of hydraulic downhole motors of different types of the same diameter 240 mm (9 ½ ″) and the same length 10 m, used for work with the above-mentioned bit types (screw motor for tricone bit and PDC bit and turbodrill for diamond bit) are analyzed. All the hydraulic downhole motors under study require fluid flow of 0.06 m 3 /s and fluid density of 1,200 kg/m 3 . At specified bit axial load values, turbodrill and screw motor provide an operating mode which corresponds to the drilling practices of the accepted bit types. where N r – DHM hydraulic power, Wt; P – DHM pressure drop, Pa; Q – drilling fluid flow, m 3 /s. It follows that the turbodrill TO value = 0.55, the screw motor with roller bit TO value = 0.28, the screw motor with PDC bit TO value = 0.36. It should be mentioned that the efficiency factor values obtained are not maximum since they do not correspond to the so-called optimal operating mode of downhole hydraulic motors under study. Maximum efficiency factor values of high-speed turbodrills are known to range from 0.70 to 0.78 whereas in the case of low-speed screw motors these values are from 0.35 to 0.45. However, it has been calculated that despite screw motor high torque, whose value can decrease because of wear, screw motor has lower energy efficiency than turbidrill owing to low rotation rate. Where L – DHM length, m; l 0 – conditional factor equal to 100 m. The calculated K L factor values are also shown in Table 1 . We can see that if all the downhole motors under study have the same length (10 m), energy efficiency of turbodrill is higher than that of screw motor, which is again accounted for by turbodrill's increased rotation rate. Different technical characteristics of turbodrills and screw motors influenced the choice of areas of their effective use. Being high-speed downhole motors, turbodrills found wide application in the second half of the 20th century in large-scale drilling in Volga-Ural region, and further in Western Siberia. The most common type of rock-cutting tools used then was tricone bit with "open" bearings working in high speed mode. Also, when penetrating deep intervals in hard rocks, diamond bits were used. The relative volume of penetration by turbodrills made up more than 80%. Turbodrills were used in various geologic and technical conditions and at different well depths. Turbodrills developed at VNIIBT are known to have set the world record in drilling a super deep Kola well 12,262 m deep. All kind of drilling muds have been applied as drilling fluid in different fields: technical water, light clay and clayless mud, heavy mud, oil-base mud. Turbodrill has almost no limitation for the temperature in place. Its rubber-covered parts can be replaced by metallic and hard-alloy ones, which allows using turbodrill at a temperature of more than180 °C. Turbodrills installed in the units for reactive turbine drilling and rotary turbine drilling made wellbores up to 5 m in diameter. Turbodrills provide high speed and positive technical and economic indicators in work with roller bits with unsealed bearings. However, today this technology is not applied widely because of the low efficiency of these bits when drilling intervals more than 1,500 m deep. The best results in using high-speed turbodrills are achieved through drilling with scraping-cutting bits without bearings provided with synthetic or natural diamonds in intervals deeper than 3,000 m. This conception corresponds to the main feature of turbodrill as a high-speed hydrodynamic downhole motor providing high penetration rate per run in hard and very hard rocks including abrasive layers [ 7 ]. For example, in Belarus high power turbodrills made in Russia with diamond bits manufactured abroad are widely used providing mechanical rate of penetration of 1.5 – 2.8 m/hr at a depth up to 5,000 m. Development and wide application of tricone bits with sealed oil-filled bearings required using a low-speed drive for the bit. PDM met these requirements. Before, use of bits with sealed oil-filled bearings was limited since they had very law service life when operating by high-speed turbodrill (400-600 rpm). Numerous attempts to design bits with oil-filled bearings for such application were not successful. It should be noted that in the beginning of PDM implementation in Russia, its low reliability and poor performance hold back large-scale deployment. Rotor-stator couple failure occurred after 20 – 60 hrs run. As a result of long-term R&D and experimental work done at VNIIBT (M.T. Gusman, D.F. Baldenko and others) and its Perm branch (Yu.A. Korotayev and others), along with the experience accumulated abroad, the design of Russian screw motor got its present form and now dominated in large-scale drilling [ 4 , 5 ]. Development of high-productivity cutting-chipping PDC bits also led to wider application of screw motors because modern low-speed PDM have increased torque compared to high-speed turbodrills. In drilling soft and medium rocks in West Siberian fields screw motors provide for 10,000 to 15,000 m penetration by one PDC bit. Screw motors design features restrict their use with heavy drilling muds (density of more than 1,500 kg/m 3 ), high temperature in place (more than 140 °C), oil-base muds and aggressive chemical agents. Also, use of screw motors requires more careful mud cleaning procedures when removing hard abrasive particles. An important advantage of screw motor compared to the so-called serial-produced multi-sectional turbodrill is its shortness. This fact played a crucial role in choosing the main technical means for directional drilling. Today, such technical means is screw motor provided with controlled inclination unit (bent sub). Development of screw motors made it possible to design and put into practice advanced drilling technologies. Today, the most widely applied large-scale drilling technology, in Western Siberia in particular, is the technology which uses screw motor with cutting-chipping PDC bits, with rotation and sliding of the drill string, which allows penetrating the specified interval in one run at the predetermined wellbore deviation rate. Application of screw motors played an important role in the development of horizontal, and multilateral drilling. The volume of horizontal and multilateral wells construction is growing significantly in Russia and throughout the world. It would be impossible without screw motors. Currently in Russia demand for turbines has declined sharply while need for screw motors is constantly increasing. The demand pattern is in much determined by regional and geological factors and also by the well design ordered by operators to drilling contractors. Today oil and gas well construction is mainly carried out in Western Siberia, in the North of the European part of Russia, and in Volga-Ural region. These are relatively shallow wells (2,500–3,500 m), without abnormal formation pressure or high temperature in place, which are mostly directional and often horizontal ones. To drill such wells PDC bits and tricone bits with sealed oil-filled bearings are used. As it was mentioned above, the most suitable type of bottom drive to these bits are screw motors. Turbodrills are mainly used with tricone bits with open bearings in top-hole drilling as well as with diamond bits which do not find wide application. Besides, rigid requirements for ensuring the predetermined well profile make drillers employ bottomhole telemetry systems which can successfully operate with short screw motors. In workover operations, in drilling of second wellbore, small-sized screw motors are widely used. All this boosts demand for screw motors. If hydrocarbons in Russia are produced commercially in other geological conditions, the pattern of demand for DHM may change. It is most likely that there will be need for downhole motors designed for work at great depths, high temperatures in place (more than 150 °C) and low flow rate of increased density drilling mud. Well drilling using downhole hydraulic motors developed in conditions of dialectical unity of two essentially different types of downhole hydraulic motors: turbodrills and screw motors (PDM). The contradictions resolved, modern turbodrills and screw motors have become more sophisticated hydraulic machines having higher reliability, utility and efficiency indicators. Turbodrills and screw motors have different characteristics, specific advantages and drawbacks, but at the same time they are technical means of one and the same oil and gas well drilling method. A wide variety of technical and energy characteristics of downhole hydraulic motors of the two main types allows realizing optimal drilling modes with bits of different types, providing the specified well spatial configuration and extending the possibilities of drilling with DHM. The areas of effective applications of turbodrills and screw motors mainly depend on the types of drill bits used in drilling. At present, for effective application it is recommended: to apply turbodrills in: drilling with diamond bits, including impregnated ones; drilling with roller bits with unsealed bearings; drilling of high-temperature wells with diamond bits; to apply screw motors in: drilling with roller bits with sealed oil-filled bearings; drilling with cutting-chipping PDC bits. This paper was selected for presentation by an SPE program committee following review of information contained in an abstract submitted by the author(s). Contents of the paper have not been reviewed by the Society of Petroleum Engineers and are subject to correction by the author(s). The material does not necessarily reflect any position of the Society of Petroleum Engineers, its officers, or members. Electronic reproduction, distribution, or storage of any part of this paper without the written consent of the Society of Petroleum Engineers is prohibited. Permission to reproduce in print is restricted to an abstract of not more than 300 words; illustrations may not be copied. The abstract must contain conspicuous acknowledgment of SPE copyright. 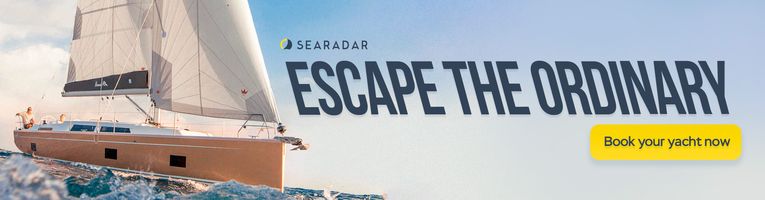 Nomenclature– screw motor. – downhole hydraulic motor. – efficiency factor. –cutting-chipping bits with diamond-insert cutters. 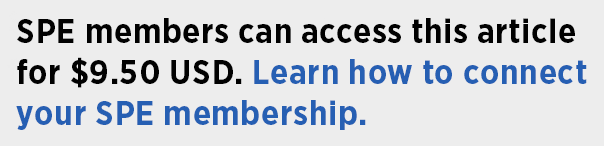 Email AlertsSuggested reading, affiliations. - Conferences
- Content Alerts
- SPE Member Pricing
- Terms of Use
Sign In or Register to ContinueSign In or Register 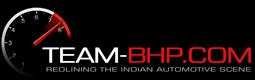 - Hot Threads
- Spare Parts
- Buy Accessories
- Classifieds
6th September 2014, 19:39 | | | Thanks | | (1) Thanks | The following BHPian Thanks ad3952n for this useful post: | | 6th September 2014, 23:04 | |
| , I have only one question for you. Why ? 7th September 2014, 11:11 | | | Link: Thank you. | | (1) Thanks | 7th September 2014, 11:34 | |
|  The following BHPian Thanks CrAzY dRiVeR for this useful post: | |  Immersive tour-performanceFollow the main character, listen to her thoughts and discover moscow, unusual genre, s onic introduction to russian culture, one-of-a-kind experience which combines a theatre play and a sightseeing tour, cinematic sound design with a binaural twist (3d sound experience), russian case 2020, the golden mask national theatre award and festival, the best walk around moscow, laureate of polar star 21' professional competition for moscow companies in tourism, have you ever wondered how you would see the world if you were from a different culture what peculiar similarities and unexpected differences would you discover in this case, does the enigmatic 'russian soul' really exist to discover these answers, we invite you to follow sasha — a russian girl and the principle character of invisible moscow. let her voice narrate a simple walk and for a short while make your eyes her eyes and make her stories into your memories. invisible moscow is a performative journey for 30 people. it is a site-specific walk for those who find themselves confined inside a tour bus. it lifts the curtain on the actually important, and thus hidden, landmarks in only 100 minutes. it is an experience to impress the first-timers and to surprise the frequent guests.. - Everyone will love this show! And native Muscovites, and city guests, and tourists (5 languages are available), both loners and companies. Invisible Moscow is an ideal combination of performance, excursion and promenade.
- An an invigorating and creative antidote to boring guided tours! Following the main character, interacting with her, the audience becomes full participants in the story. This turns the walk into a deep existential experience.
- Tourism + Technology = New Moscow Attraction. The experience is undeniably engaging and insightful! The guide is the fictional character of Sasha, a journalist stood up by her friends. Unbeknownst to her, we tourists follow her as she looks to fill her time in Moscow. As she chats to herself, the headphones relay Sasha's stream of consciousness – available in Russian, English, German and French – directly into the visitors' ears.
Just put on your headphones and follow the heroine. Her voice will guide you through the most well-designed stage set — the streets of Moscow. Feel free to observe, eavesdrop, and play with the surroundings (we won't tell anyone, promise)!To be immersed means to be in-sync with oneself, not the others.. - to choose an alternative date and time for the performance;
- to get your money back.
- Event cancellation;
- The original event was replaced with a different one;
- The event was postponed or rescheduled.
 Navigation MenuSearch code, repositories, users, issues, pull requests..., provide feedback. We read every piece of feedback, and take your input very seriously. Saved searchesUse saved searches to filter your results more quickly. To see all available qualifiers, see our documentation . - Notifications You must be signed in to change notification settings
Immersive Petroleum Can't Install Mods to Motoboat While Playing on Server #385 beldroy commented Jul 28, 2018 : 1.4.1 : Can't install mods to Motorboat from "Immersive Petroleum"while playing on server but there is no problem with this while playing in singleplayer. : It is repetable while on server. | The text was updated successfully, but these errors were encountered: |  tfox83 commented Sep 17, 2018 This has been reported, as soon as a fix is out I will get it in the pack ASAP | Sorry, something went wrong.  No branches or pull requests  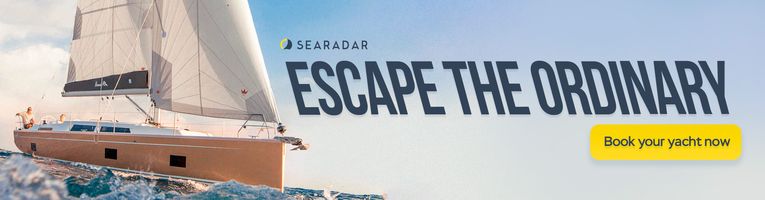 | | | |
IMAGES
VIDEO
COMMENTS
The Motorboat is an item and vehicle added by Immersive Petroleum. It is an upgrade to the vanilla Minecraft Boat and is powered by Gasoline. The Motorboat can store up to 8,000 mB of a valid fuel, which can be input by right clicking on the boat while not riding it. It stores this fuel when broken. While moving forward or backward, the Motorboat consumes 1 mB of fuel per tick. If the player ...
Immersive Petroleum is a lightweight content add-on for Immersive Engineering that introduces oil, oil extraction, and oil processing to the mod's tech progression. It includes an expansive set of configuration options to ensure that it will be a welcome addition to any modpack that includes Immersive Engineering. Mod Information.
Immersive Petroleum is an Immersive Engineering addon created by Flaxbeard. The mod adds Oil alongside means of extracting and processing Oil. The mod is available for Minecraft versions between 1.10.2-1.12.2 and 1.16.4 Immersive Petroleum on CurseForge Immersive Petroleum on GitHub
1: Place the motorboat in the vice slot of the workbench. 2: Place the upgrades in the three slots that show up. I can't seem to find a button that says "Confirm you want this and put these upgrades on the boat." you find out yet? Here's what I'm doing: 1: Place the motorboat in the vice slot of the workbench. 2: Place the upgrades in the three ...
It's missing from the crafting menu, in addition Lubricant does not seem to do anything or use up from the can when 'applying' to machines, and the gasoline powered portable generator also is buggy and does not work. Only use for gasoline is fuel for the chemical thrower in the latest version of immersive petroleum, and i see no use for ...
Using the motorboat from Immersive Petroleum, upgraded with Emergency Paddles and Reinforced Hull, you can get around the Nether pretty quickly, no gasoline required. The boat and those two components are actually pretty cheap, the boat being treated wood and some iron components, the paddles being just treated wood, and the hull being a bit of ...
Bug Report Immersive Petroleum Motorboat does not properly use upgrades (Emergency paddles., Expanded Fuel Tank etc.). You can add them through Engineer's Workbench, but when the boat is placed in the world, the default is used instead o...
Bug Report Immersive Petroleum Motorboat does not properly use upgrades (Emergency paddles., Expanded Fuel Tank etc.). You can add them through Engineer's Workbench, but when the boat is placed in the world, the default is used instead o...
Things included in the first version of Immersive Petroleum: Pumpjack and Distillation Tower; Portable Generator; Lubricant Can; Automatic Lubricator; Motorboat; Projectors; Asphalt paving; Immersive Petroleum Mod will add new Multiblock machines from Oil Derricks to Cokers that can smash Bitumen into Diesel and Petcoke. You can use the mod in ...
Gasoline is a fuel added by Immersive Petroleum. It is similar to Diesel but is most suitable for small engines. It is created in the Distillation Tower . Gasoline can be used to power a Portable Generator to produce Redstone Flux, or can be used to fuel a Motorboat . Community content is available under CC BY-NC-SA unless otherwise noted ...
ImmersiveEngineering-.12-82.jar immersivepetroleum-1.12.2-1.1.9.jar. It seems that despite putting upgrades into a motor boat it will not upgrade the boat, I can't really even tell if the boat has the upgrades installed or if they're in some weird worktable limbo inventory.
Immersive Petroleum Optimal Setup with Oil (1.12.2) I have calculated the most realistically optimal setup. 5 Pumpjacks (4 with lubricant) 3 Distillation Towers. 5 + 1 Diesel Generators. 14,760.4 net positive rf at 305% efficiency. 15,784.4 net positive rf at 357% efficiency with lubricant. Using numbers from the wiki this comes out the be the ...
GeradesoLukas commented on Dec 13, 2020. So I tried to get a motorboat and I just could not find the item. Also, I tried to summon it using the following command and the entity turns out to be completely invisible. /summon immersivepetroleum:speedboat.
This article, written by Assistant Technology Editor Karen Bybee, contains highlights of paper SPE 117386, "Application of Permanent-Magnet Motors in Oil Production," by Igor Azanov and Arthur Shamigulov, TNK-BP, originally prepared for the 2008 SPE Russian Oil and Gas Technical Conference and Exhibition, Moscow, 28-30 October.
Abstract. In Russia oil and gas wells are mainly drilled with downhole hydraulic motors (DHM).In the second half of the 20th century turbodrills, which are high-speed downhole motors, found wide application in large-scale drilling in Volga-Ural region, and further in Western Siberia. The most commonly used type of rock-cutting tool was a tricone bit with
RP-1 (alternately, Rocket Propellant-1 or Refined Petroleum-1) is a highly refined form of kerosene outwardly similar to jet fuel, used as rocket fuel. RP-1 has a lower specific impulse than liquid hydrogen (LH2), but it is cheaper, stable at room temperature, far less of an explosion hazard, and far denser.
The same has been shown at the Moscow Motor Show 2014. INFO Thanks (1) Thanks 6th September 2014, 23:04 #32: khoj. Senior - BHPian . Join Date: Sep 2008. Location: Dilli. Posts: 2,718 Thanked: 1,287 Times View My Garage ...
Immersive petroleum motorboat seem to crash my game back to log in. Expected Behavior. Me travling via boat without problems. Steps to Reproduce (for bugs) 1.Make motorboat 2.Fuel motorboat with gasoline 3.Hop on and ride to crashdom. Context. I never made a motorboat so I made one to try it out, but to only find that I crash as soon took off.
Invisible Moscow is a performative journey for 30 people. It is a site-specific walk for those who find themselves confined inside a tour bus. It lifts the curtain on the actually important, and thus hidden, landmarks in only 100 minutes. It is an experience to impress the first-timers and to surprise the frequent guests.
Add a Comment. Javi137 • 3 yr. ago. Hello! In order to start with the basics of mekanism, you need some sort of power generation, so IE is probably your best bet for starting. You will also need steel, which IE provides. Start with IE, get some steel, get some power (water wheel, wind turbine and so on) and then you can start with mekanism. 1.
Modpack Version: 1.4.1 Issue: Can't install mods to Motorboat from "Immersive Petroleum"while playing on server but there is no problem with this while playing in singleplayer. Is it Repeatable?: It is repetable while on server.